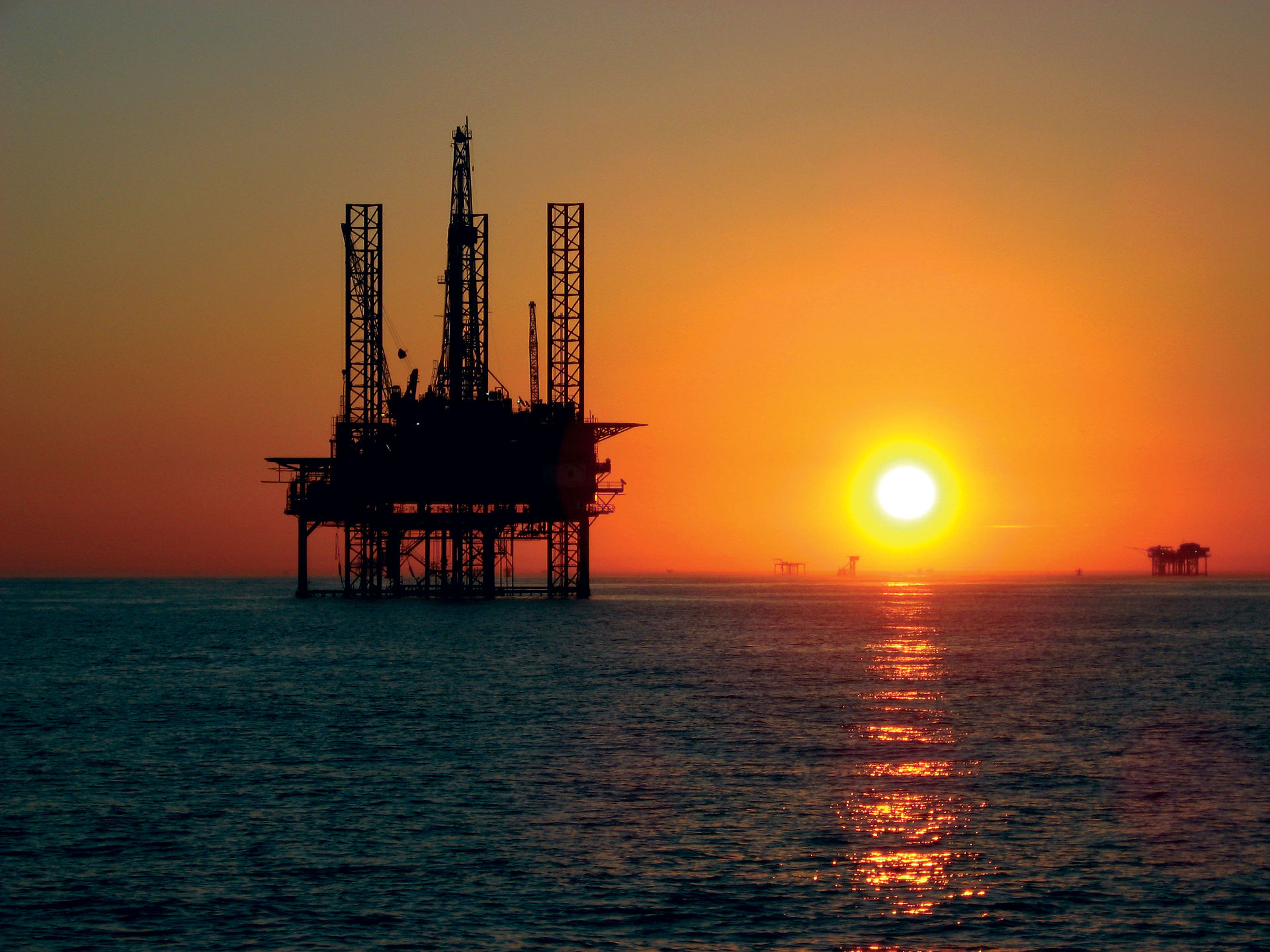
Bytes engineering design concultancy

Globel Engineering Service Provider
Maintenance and Inspection: operation of heat exchangers
Maintenance and inspection are crucial aspects of ensuring the safe and reliable operation of heat exchangers in distillation columns design services. Here's how maintenance and inspection activities are typically carried out:
-
Routine Inspection: Conduct regular visual inspections of the heat exchanger and its associated components to identify any signs of corrosion, erosion, leakage, or mechanical damage. Inspect seals, gaskets, flanges, and connections for integrity.
-
Non-Destructive Testing (NDT): Perform non-destructive testing techniques, such as ultrasonic testing, radiographic testing, magnetic particle testing, and dye penetrant testing, to detect defects, cracks, or corrosion in the heat exchanger components without causing damage.
-
Cleaning: Regularly clean the heat exchanger surfaces to remove fouling, scale, deposits, or other contaminants that can impair heat transfer efficiency. Use appropriate cleaning methods, such as chemical cleaning, mechanical cleaning (e.g., brushing or scraping), or water jetting, based on the type and severity of fouling.
-
Tube Inspection: For shell-and-tube heat exchangers, inspect the condition of the tubes for fouling, corrosion, erosion, or tube wall thinning. Use techniques such as eddy current testing, remote field testing, or internal visual inspection tools to assess tube integrity.
-
Pressure Testing: Periodically perform pressure testing of the heat exchanger to verify its structural integrity and leak tightness under operating conditions. Conduct hydrostatic testing or pneumatic testing in accordance with applicable standards and regulations.
-
Seal and Gasket Replacement: Replace seals, gaskets, and packing materials as needed to maintain leak-tight seals and prevent fluid leakage. Ensure that replacement components are compatible with the process fluids and operating conditions.
-
Lubrication and Maintenance of Moving Parts: Lubricate bearings, gears, shafts, and other moving parts as per manufacturer recommendations to prevent friction, wear, and mechanical failures. Inspect and replace worn or damaged components as necessary.
-
Instrument Calibration: Calibrate instrumentation and control devices, such as pressure gauges, temperature sensors, flow meters, and level indicators, to ensure accurate measurement and control of process parameters.
-
Documentation and Record-Keeping: Maintain detailed records of maintenance activities, inspections, repairs, and any deviations from normal operating conditions. Document findings, recommendations, and corrective actions for future reference and analysis.
-
Training and Qualification: Provide training to maintenance personnel on proper maintenance procedures, safety practices, and equipment operation. Ensure that personnel are qualified and competent to perform maintenance tasks effectively and safely.
By implementing a comprehensive maintenance and inspection program, operators can detect potential issues early, prevent unplanned downtime, extend the service life of the heat exchanger, and ensure the safety and reliability of the distillation column operation.
You
Instrument Calibration:
Instrument calibration is essential for ensuring the accuracy and reliability of measurement and control instruments used in distillation column operations. Here's how instrument calibration is typically carried out:
-
Establish Calibration Procedures: Develop detailed calibration procedures for each type of instrument used in the distillation column, including pressure gauges, temperature sensors, flow meters, level indicators, and analytical instruments. The procedures should outline the calibration method, frequency, standards used, and acceptance criteria.
-
Select Calibration Standards: Identify appropriate calibration standards or reference instruments with known accuracy and traceability to national or international standards. Calibration standards may include certified pressure calibrators, temperature baths, flow calibration rigs, or calibration gases. distillation columns design services
-
Calibration Intervals: Determine the calibration intervals based on factors such as the manufacturer's recommendations, regulatory requirements, industry best practices, and the criticality of the instrument to the process. Critical instruments may require more frequent calibration than non-critical ones.
-
Perform Calibration: Conduct calibration activities according to the established procedures and using the selected calibration standards. Calibrate each instrument at multiple calibration points across its operating range to ensure accuracy and linearity. Record calibration results, including deviations from expected values and any adjustments made.
-
Adjustment and Recalibration: If calibration results indicate that an instrument is out of tolerance, make necessary adjustments to bring it into compliance with the specified accuracy criteria. Repeat the calibration process as needed until the instrument meets the required performance standards.
-
Documentation: Maintain detailed calibration records for each instrument, documenting calibration dates, results, adjustments, and any maintenance or repairs performed. Ensure that calibration certificates are issued for calibrated instruments, providing traceability to the calibration standards used.
-
Calibration Traceability: Ensure traceability of calibration to national or international standards by using accredited calibration laboratories or calibration equipment with documented traceability chains. Maintain records of calibration traceability to demonstrate compliance with regulatory requirements and quality standards.
-
Calibration Management System: Implement a calibration management system or software to schedule, track, and manage calibration activities for all instruments in the distillation column. The system should provide reminders for upcoming calibrations, maintain calibration history, and generate reports for auditing purposes.
-
Training and Competency: Provide training to personnel involved in instrument calibration to ensure they understand the calibration procedures, techniques, and quality standards. Ensure that calibration technicians are qualified and competent to perform calibration tasks effectively and accurately.
By following these calibration best practices, operators can ensure that measurement and control instruments in the distillation column are properly calibrated, providing accurate data for process control, optimization, and compliance with regulatory requirements.
You
Calibration Management System
distillation columns design services
A Calibration Management System (CMS) is a software solution designed to streamline and automate the management of calibration activities for instruments and equipment across an organization. Here's an overview of the key features and benefits of a CMS:
-
Instrument Database: A CMS typically includes a centralized database to store information about all instruments and equipment requiring calibration. This database contains details such as instrument type, serial number, location, calibration history, calibration intervals, and calibration standards used.
-
Calibration Scheduling: The CMS allows users to schedule calibration activities based on predetermined intervals, manufacturer recommendations, regulatory requirements, or specific operational needs. It provides reminders and notifications for upcoming calibrations to ensure timely completion.
-
Work Order Management: Users can generate work orders for calibration activities, specifying the instruments to be calibrated, the calibration procedures to be followed, and any special instructions or requirements. Work orders can be assigned to calibration technicians and tracked throughout the calibration process.
-
Calibration Procedures: The CMS provides access to standardized calibration procedures or work instructions for each type of instrument or equipment. These procedures outline the steps to be followed, calibration methods, calibration standards required, and acceptance criteria.
-
Calibration Certificates: After calibration is completed, the CMS generates calibration certificates documenting the calibration results, deviations from expected values, adjustments made (if any), and the traceability of calibration standards used. Calibration certificates provide evidence of compliance with quality standards and regulatory requirements.
-
Traceability and Audit Trail: The CMS maintains a comprehensive audit trail of all calibration activities, including calibration dates, results, personnel involved, and any changes made to calibration records. This traceability ensures accountability and facilitates auditing and compliance verification.
-
Reporting and Analysis: Users can generate various reports and analytics to monitor calibration performance, track instrument status, identify trends, and analyze historical data. Reports may include calibration status, overdue calibrations, calibration history, and equipment reliability metrics.
-
Integration with Asset Management Systems: Many CMS platforms offer integration capabilities with asset management systems, maintenance management systems, and other enterprise software solutions. This integration enables seamless data exchange and ensures alignment between calibration activities and overall asset management processes.
-
Compliance Management: The CMS helps organizations ensure compliance with relevant quality standards (e.g., ISO 9001) and regulatory requirements (e.g., FDA, EPA). It provides tools for documenting compliance, managing non-conformities, and preparing for audits or inspections.
-
Training and Competency Management: Some CMS platforms include features for managing training records and competency assessments for calibration technicians. This ensures that personnel responsible for calibration activities are adequately trained and qualified to perform their roles effectively.
Overall, a Calibration Management System streamlines calibration processes, improves efficiency, enhances data accuracy, and helps organizations maintain compliance with quality standards and regulatory requirements.
ChatGPT can make